Volumetric Feeder vs Gravimetric Feeder
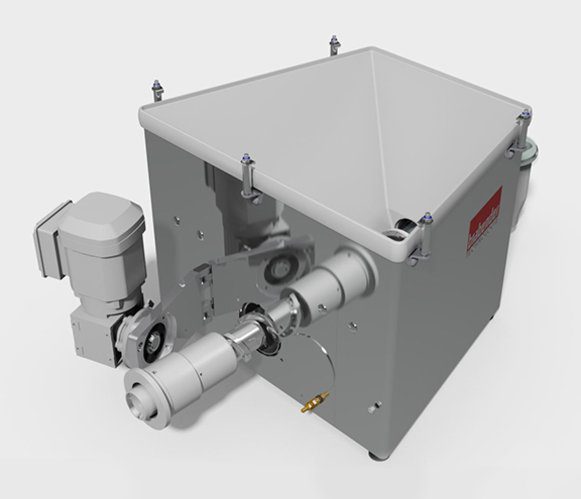
One of the most common questions we get asked by those new to feeding raw materials is “what is the difference between a volumetric and a gravimetric feeder?”
If you read this short overview, we will explain the pros and cons of each approach.
Volumetric Feeding
As the name suggests, a volumetric feeder works based on the volume a material occupies. Mechanically they are typically a single or twin screw feeding configuration and as the screw rotates, a certain volume of material is collected in the feed trough. This is then pushed forward by the screw or screws and exits through the outlet tube to the downstream process equipment.
Liquid pumps work in a similar way, as they pump, they move a volume of liquid forward through the pipework.
The problem with this approach is that if the feeder is empty, the machine itself doesn’t “know” that controls are designed around the motor driving the screws, they will rotate at more or less an identical rate irrespective of how much material is on the feeder.
Similarly if the material changes density, bridges above the feed trough or changes its flow behaviour there will be no reaction from the control system. It will keep running at the same speed, delivering the same “volume” until an external operation either speeds it up or slows it down.
Gravimetric Feeding
Gravimetric feeders incorporate a volumetric feeding device into a more sophisticated system that works based on the mass of the material being fed.
A weighing system, either a weigh scale or an arrangement of load cells, weighs the hopper, feeder and material and passes this onto a controller that can then calculate the amount of material being fed in Kg/Hr or similar units. Or if a belt is the feeding mechanism, it is the belt and the material sat on it that is weighed.
This allows the feeder to be set to a specific “Setpoint” feedrate and the control system will speed the feedrate up and down with any material variations to achieve this target rate.
If the rate drops away too far from target, alarms can be raised and the process brought to a controlled stop if necessary, while the problem is fixed.
Applications for Volumetric Feeders
Where accurate material flow is not critical, then a volumetric feeder can be ideal, for example as a bag filling device. The bag weighing system can switch the feeder on and off or set it to a dribble rate if required, but second by second feeding accuracy is not typically required.
Refilling a loss-in-weight feeder is another regular application. The downstream feeder will control the input and the volumetric feeder will provide a controlled refill which is ideal if the material tends to compact if dropped directly into the feeder.
Essentially volumetric applications can be thought of the same way as any conveying task, you need to move your raw material from one point to another at a consistent rate but accuracy of feed is not critical to the process.
Gravimetric Feeding Applications
There are two broad categories of gravimetric feeders: loss-in-weight and weighbelt feeders. Both offer greater accuracy than volumetric feeders, but the downside of this is that both will cost more as they include weighing systems and sophisticated controllers.
Extrusion is a very common application for loss-in-weight feeders. Multiple ingredients have to be fed into the extrusion process and accuracy is of critical importance to the end product quality in many processes.
Pharmaceutical and food production also have many production processes where accuracy is key and in addition to this, traceability must be maintained. Gravimetric feeders allow processors to record the exact ingredients used in their processes and build the necessary quality control records to meet local legislation requirements.
So for gravimetric applications a processor is typically seeking to minimise overuse of key ingredients, maintain quality, feed accurately to a recipe or implement a sophisticated control system for remote operation.
In Conclusion
Although we talk about volumetric and gravimetric feeders, perhaps the easiest way to decide which is the right one for you, is not to think about the feeder mechanically that is often the same device, but to think about how much control you need.
If you need a lot then it’s going to have to be a gravimetric feeding system. If you don’t need that much and just need a device to control the flow, then volumetric may well be enough.
As always, if you do have a question, or a tricky application, in most cases the team at Genesis will have solved it successfully before. So give us a call or drop us an email and we can hopefully save you some time deciding which is right for your production process.