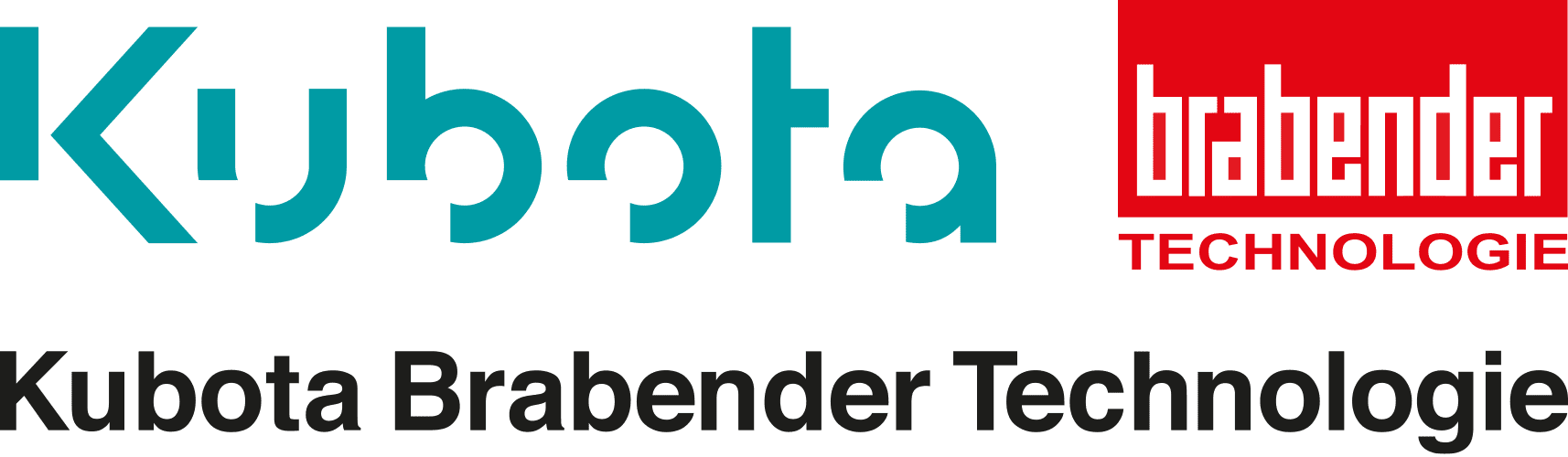
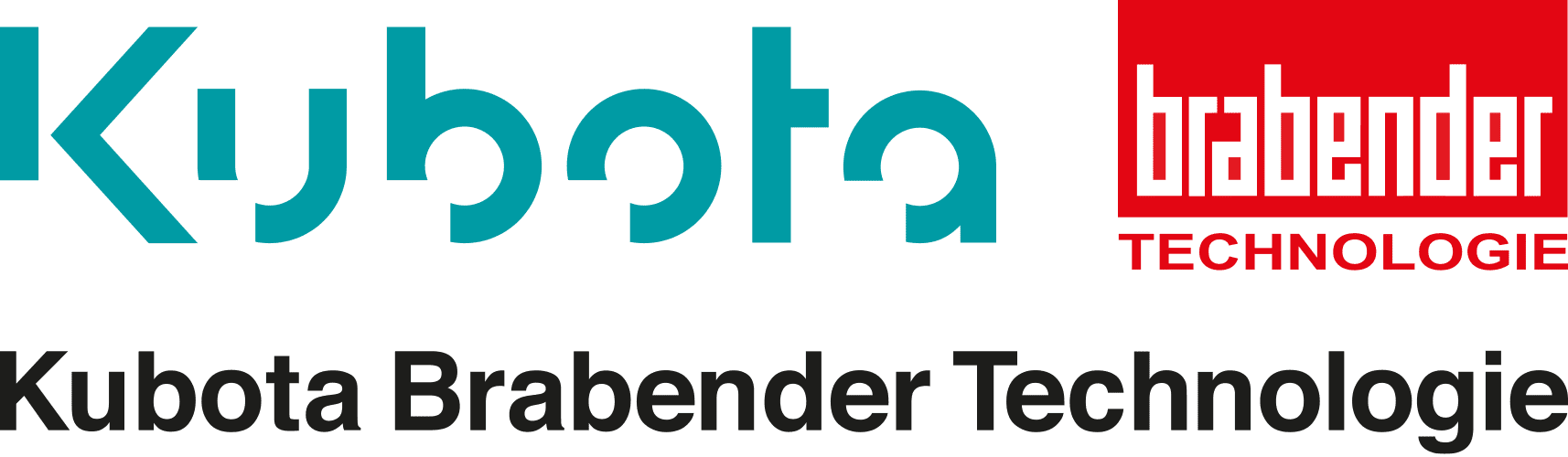
Genesis Process Solutions are bulk material handling experts for the food, plastic, chemical, detergent and pharmaceutical industries.
Brabender systems for feeding, weighing, discharging and flow metering of bulk ingredients and fluids can be used for a huge variety of industrial processes. For example in the plastics, chemical, pharmaceutical, food, pet food, detergent, ceramics, glass or construction material industries as well as in numerous other industries.
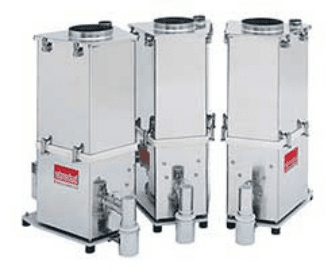
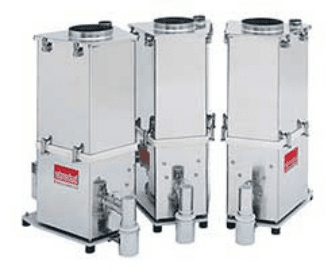
The Brabender Technologie Flexwall feeder has been in the market place since 1994 and is the perfect choice for both free flowing and poor flowing products. Whether you are looking to feed a sticky powder, a free flowing granule, a light and fluffy powder, regrind or even fibre glass strands, the Flexwall feeder range should be chosen to ensure hassle free feeding.
The Flexwall range of feeders are available as both volumetric feeders and gravimetric feeders.
The Flexwall feeder has a polyurethane trough which is externally massaged to ensure the product in the feeder is sufficiently agitated so as to achieve the best mass flow.
Another advantage of the polyurethane trough and external massage paddles is that the product does not come in to contact with a mechanical agitator like in conventional feeders so for products that have a low melting point it is the perfect feeder for gently dosing the ingredient without working it too much. The same principle applies to food ingredients, as the Flexwall feeder creates real mass flow - using the first in, first out principle, the ingredients are not held within the feeder and stuck to agitators like conventional screw feeders.
One more significant benefit of the Flexwall feeder is how easy it is to clean. Once the hopper, screw and tube has been removed, the flexible trough can be removed from the feeder and taken to a cleaning area or swapped with another trough ready to go. It only takes a matter of minutes to clean down the Flexwall feeder meaning changeovers and downtime are kept to a minimum.
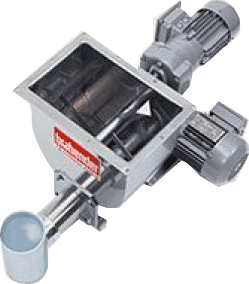
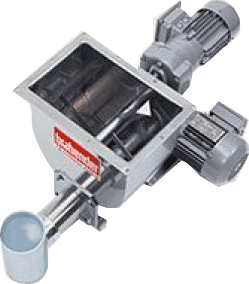
The Brabender Technologie range of single screw feeders are designed to feed at rates of 500g/hr up to 20 tonnes/hr.
With screw sizes starting from 13mm diameter and up to 300mm diameter, the screw feeders are designed for feeding ingredients at a very wide feed rate range.
All of our "DSR" range of feeders have a stainless steel screw trough, fabricated from 304 stainless steel ( optional 316 stainless ) with an integrated rotating agitator blade, designed to stir the ingredient to aid flow in to the dosing screw. Various screw designs and different agitator blades are available to ensure the best possible feeding from the DSR range.
The Brabender screw feeders are well renown for being incredibly accurate, flexible and durable, even in some of the most heavy duty industries.
All of the single screw feeders are available with various extension hoppers and are available with volumetric or gravimetric controls.
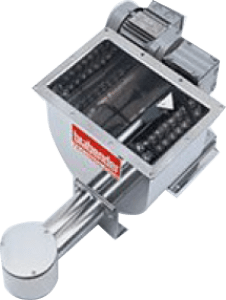
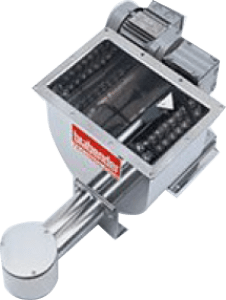
The Brabender Technologie range of twin screw feeders are designed to feed at rates of 50g/hr up to 10 tonnes/hr.
With screw sizes starting from 12mm diameter twin screws up to 100mm diameter, the screw feeders are designed for feeding ingredients at a very wide feed rate range.
All of our "DDSR" range of feeders have a stainless steel screw trough, fabricated from 304 stainless steel ( optional 316 stainless ) with an integrated rotating agitator blade, designed to stir the ingredient to aid flow in to the dosing screw. Various screw designs and different agitator blades are available to ensure the best possible feeding from the DDSR range.
Brabender twin screws are used where materials can be floodable or not suitable for the Flexwall range of feeders. The double screw design ensures a large opening in which to get product in to the screws.
The Brabender twin screw feeders are well known for being incredibly accurate, flexible and durable, even in some of the most heavy duty industries.
All of the single screw feeders are available with various extension hoppers and are available with volumetric or gravimetric controls.
GRAVIMETRIC FEEDERS
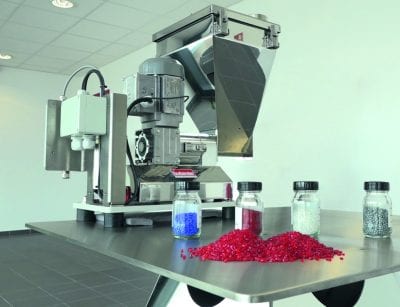
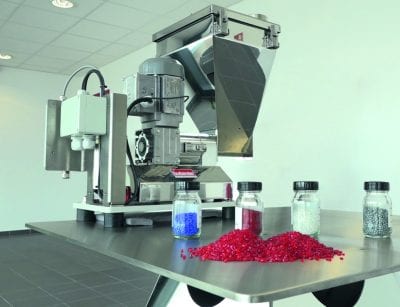
When accuracy and repeatability is essential, Brabender Technologie offer a wide range of gravimetric feeders. The complete range has been designed to suit most applications in all of the main industry sectors. With feed rates from as little as 30g/hr up to 50te/hr you can be sure that we have a gravimetric feeder to suit your specific requirements.
Gravimetric feeding is typically done in two ways:
- LOSS-IN-WEIGHT - Weight loss in measured by means of a loadcell system. As the feeder is running, the weight loss is compared against the setpoint and the speed is adjusted in order to maintain the feed rate at the required setpoint. The Brabender range of Congrav controllers ensures an accurate feed rate. Both continuous feeding and batch feeding options are available.
- GAIN-IN-WEIGHT - With gain-in-weight applications, our volumetric feeders are used to dose into a weigh hopper and the increase in weight is monitored. The Brabender Congrav control system is used to monitor the increase in weight and alter the speed of the feeder accordingly to achieve the best possible accuracy.
There are variations to the options above, bespoke systems can be designed and supplied to suit your specific needs.
With gravimetric feeding, the refilling of the equipment is extremely important and the correct design should be used in order to maximise the performance of the gravimetric feeder. In order to help you achieve this, Genesis now offer a full range of refill systems, all of which can be tailored to your specific needs.


Genesis Process Solutions offer a wide variety of loss in weight feeders to suit most applications.
Not only do we offer Brabender Technologie feeders in all forms, single screw feeders, twin screw feeders, Flexwall feeders, vibratory feeders and liquid feeders but we now also offer bespoke
systems.
The Brabender Technologie range of loss in weight feeders cover most feed rate ranges used in industry today - starting from 50g/hr and going all the way up to 20 tonnes/hr.
Typically used in continuous production applications, such as extrusion or continuous mixers, the feeders are extremely versatile and can be linked to most refilling methods (please click here for refill systems).
As agents for Walter Krause flexible silos and Sinfimasa screw conveyors, we can also offer these as part of a bespoke loss in weight system.
We also offer traditional style steel and aluminium hoppers and can fit them with screw conveyors, rotary valves or other metering devices and use them as a loss in weight system.
For incredibly accurate requirements, we would offer digital loadcells and integrate them into a Brabender control system.
For higher throughputs and bespoke systems we would use analogue loadcells with intelligent amplifier systems which can be linked to a Brabender control system or a bespoke PLC.
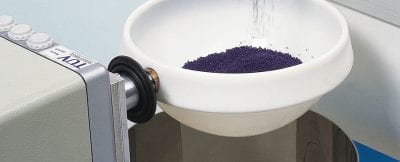
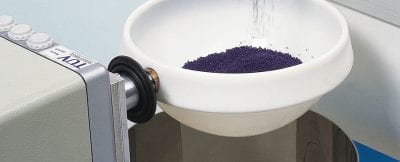
Genesis Process Solutions offer gain-in- weight systems where a loss-in- weight system is not suitable.
Gain in weight systems are primarily used in batch applications whereby a receptacle of some sorts is filled to a pre-selected weight.
With gain in weight systems, you can only add one ingredient at a time so if time is critical, we recommend a loss in weight batch system.
With gain in weight systems we can integrate most filling forms in to the system, whether it is a Brabender volumetric feeder, screw conveyor, belt conveyor or rotary valve.
Control of the system can either be via a Brabender control system or a bespoke PLC, usually dependant on customer requirements and what functionality is required.


Brabender Technologie GmbH & Co. KG have supplied control systems for their equipment for well over 60 years !
Specializing in feeding systems, the control systems available are designed to give reliable and repeatable performance across the full Brabender range of feeding technology.
Various control systems are available ranging from volumetric feeder controls, loss-in-weight feeder controls, batching system controls to full integration with customer's plant control.
As technology changes at such a rapid pace, Brabender endeavour to move with it and a dedicated department are constantly looking at ways in which to improve not only the Brabender systems but into things like integration to other systems.
Brabender's latest range of feeding technology includes the Congrav touch screen range including single and multiple feeder interface modules.
For the actual control of the feeders, there are panel mount control board options called Congrav CBplus which have in-built interfaces available for connection to other systems. There is also the option to have the control modules mounted on the feeder to reduce installation and panel costs, these are the ISC-CMplus range.
Additional feeders can be added at a later date if required very simply using Brabender's BUS system.
BELT FEEDERS
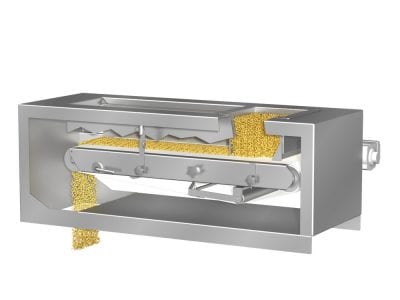
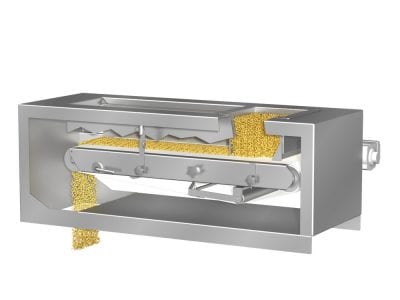
Brabender Technologie GmbH & Co. KG manufacture a wide range of Belt Feeders, suitable for use in the food, plastic and chemical industry sectors.
The belts are available in several sizes, starting from a 150mm belt width, the belt feeders can operate between 10kg/hr and 50 tonnes/hr of product depending on the size of the machine used.
The Brabender belt feeders can be used as continuous feeders, batch feeders or as a measuring belt feeder for continuous throughput measurement.
Due to an adjustable gate after the inlet to the belt, each belt feeder has a huge turndown ratio of up to 100:1.
The measuring of the product is achieved just after the gate using a loadcell, a torsion bar and weighing bridge that the product runs over on the belt. The product is weighed as it travels over the loadcell and the Brabender Congrav controller then calculates what speed the motor should run at to maintain a specific feed rate. In a similar way, the bet can be ran at a fixed speed and the loadcell is then used to indicate a throughput.
As only a small portion of the belt is weighed and not the whole of the machine, it makes installation confined areas much easier as there is not a requirement for a big refill hopper like in conventional loss-in-weight feeding.
The outer casing of the belts are manufactured from 304 stainless steel and are large enough to allow access to all working areas of the belt for ease of maintenance.
Various options are available for the Brabender belt feeders including :
- ATEX certification
- Hygienic design belts with retractable belt frame
- Belt in-feed adaptors
- Pre-feeders
- Open belt designs
VIBRATORY TRAY FEEDERS


Brabender Technologie GmbH & Co. KG manufactures Vibratory Tray Feeders, suitable for use in the food, plastic and chemical industry sectors.
Brabender vibratory feeders come in a huge range of sizes, starting from a 45mm diameter tray up to a 200mm diameter tray but are all designed in a similar modular way.
Available as Loss-in-Weight feeders only, the feeders are made up of three modules:
- The free standing weighing module consists of either a DigiMass-2 digital loadcell or an analogue loadcell housed in a stainless steel frame
- The feeding module consists of a stainless steel tray that is vibrated by an electromagnetic vibration drive featuring a vibration amplitude feedback system, which ensures linear conveyance characteristics over the entire feed rate range
- The hopper module consists of a stainless steel conical hopper as an in integral part of the rack in which the feed module is mounted
Various hopper inlets are available to suit upstream filling equipment.
Various options are available for the Brabender vibratory tray feeders including:
- ATEX certification
- Hygienic design
LIQUID FEEDERS


Brabender Technologie GmbH & Co. KG manufactures Liquid Feeders, suitable for use in the food, plastic and chemical industry sectors.
The Brabender liquid feeders are capable of metering liquids with low to high viscosities.
Available as Loss-in-Weight feeders only, the feeders are made up of three modules:
- The free standing weighing module consists of either a DigiMass-2 digital loadcell or an analogue loadcell housed in a stainless steel frame
- The feeding module consists of a pump - type dependant on the product and feed rate required
- The hopper module consists of a stainless steel conical hopper as an in integral part of the rack in which the connection to the pump is mounted
Depending on liquid characteristics and counter-pressures, the system uses one of the following dosing pumps:
- Piston Pumps
- Diaphragm Pumps
- Gear Pumps
- Hose Pumps
- Rotary Piston Pumps
- Eccentric Screw Pumps
Heated designs including electrical heating, hot oil / water heating, steam heating etc…
As an alternative to a loss-in-weight liquid system, a Coriolis Mass Flow Meter can be used in combination with an upstream dosing pump.
Both systems can be connected to the Brabender Congrav control system.
Need help finding the right product for your process?