What feeder for Fibreglass?
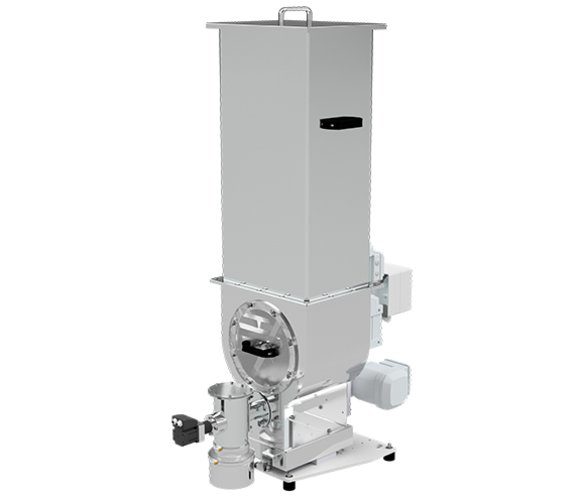
Feeding fibreglass accurately into your process can be something of a challenge. The material itself comes in many different forms, long strands, short strands, fairly free flowing, very poor flowing, and friable; fibreglass has them all.
Here’s an overview of what you need to consider about feeding fibreglass…
The length of the strands and the coating are key to how well the fibres flow. If they are coated and short they tend to flow well and can be managed by a single screw feeder with an open flight or spiral screw profile. Alternatively the gentle handling of a vibratory feeder may be ideal.
Vibratory feeders have the advantage of having more or less no mechanical action on the material being fed; this means it is the best option for gentle handling as it will cause minimal damage to the material as it passes through the feeder.
Screw feeders have at least one screw rotating in the trough and then outlet tube so will inevitably have some impact on the fibres as they pass through the machine. This can be reduced by having large clearances between the screw and walls of the tube but it cannot be fully eliminated.
If they are long fibres then a more specialist feeder such as the Brabender FiberExpert may be the best choice. This feeder is specially designed for long fibres (and not just fibreglass but any long stranded material or regrind) that tend to bind and hang up in a normal feeder.
Will the material bridge?
Before the material even arrives at the feeding device the question of bridging should be considered. A traditional feeder has steep sided walls and then an agitating mechanism above the feed trough at the bottom of the device.
Even steep walls may not be enough, you may have to consider having a vertically walled hopper. With the agitation, our Flexwall device is gentle on the product but might not be enough to prevent a bridge forming. In this case the specially designed agitator of the FiberExpert may be the answer.
A traditional agitator tends to pass close to the hopper sides in order to clear any material sticking to the walls. This may lead to the fibres jamming and breaking up so a new shape of agitator has been created by the experts at Brabender to overcome these issues.
Static cling?
Given the challenges already mentioned you might think that’s enough for one material to throw at you but fibreglass can also create a lot of static as it is fed and this can cause further issues that need to be addressed particularly in areas such as the outlet pipe arrangement. We don’t want a large ball of product forming here and either blocking the tube or falling off periodically and causing an irregular flow to the downstream equipment.
Lab Testing
Fibreglass comes in a huge range of shapes and this means lab testing is the sensible route to feeder selection. There are some common types that allow selection with the need for a test but if you really need to see how your materials will perform in as close to a production environment as we can make, then set up a test and try some different routes.
Our team has tackled many different feeding problems and is ready to help you make the best choice for your production line. Give us a call and we can take a look at your materials and let you know what we think.