What Feeder for Flour?
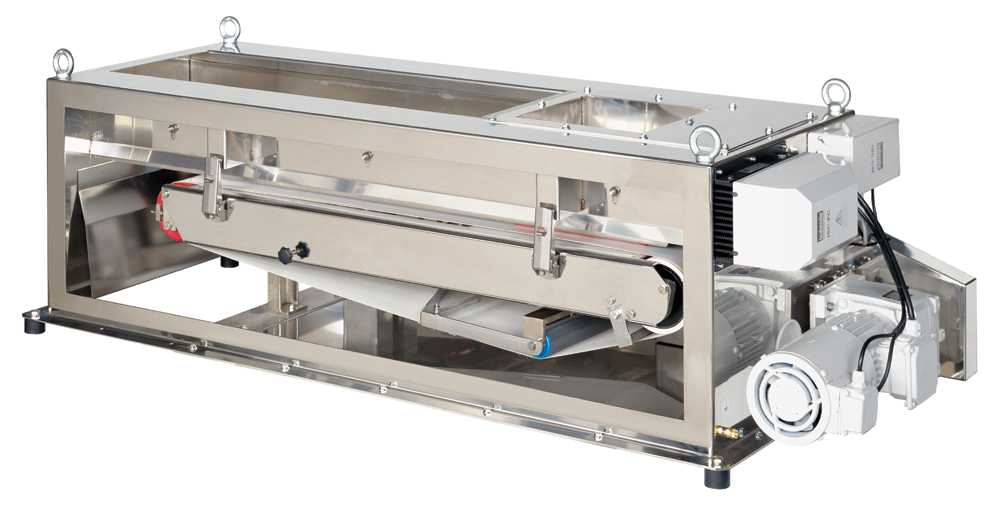
Flour is one of the most widely used materials in the food industry and can be handled by a variety of volumetric and gravimetric feeders. But what’s the right one for your application? Let’s take a look at the main factors to consider.
What type of flour?
Generally flour is a reasonably free flowing powder that can be both dusty and likely to become aerated when being moved in bulk. There are many grades of flour and hence each needs to be considered on its own characteristics and the impact of environmental factors in the surrounding processing area.
Feed Rates
For feed rates measured in tens or hundreds of kg/hr you have the option of using screw feeders with reasonably sized feed hoppers for a gravimetric feeder. For rates that go higher than this and are in thousands of kg/hr, then a gravimetric belt feeder offers a more realistic option as you do not require a large weighed hopper and the corresponding headroom that requires, to handle high throughput rates.
Another option may be suitably sized flowmeter linked to an upstream rotary valve or screw conveyor but typically a belt feeder is the choice for high rate applications.
For any system, control of the flour is important as flour moving at high rates and in volume can act very much like water as it becomes aerated and can flood through a belt feeder if care is not taken to meter the powder through a suitable device before it reaches the belt. A single screw feeder with an open flight may also suffer from this flushing effect, where a twin screw feeder will tend to control the flow better as it has intermeshing screw flights that act to hold the flour back.
Dust Control
Controlling dust and the corresponding health and explosion risks are always important where flour is being handled. Enclosed screw feeders provide a better dust control strategy than the more open belt feeders but this issue can be overcome with the correct installation and maintenance procedures. If small amounts are being handled and sack-tipping and other devices are being used, dust control systems must be installed to avoid excessive dust for operators. The HSE defines a workplace exposure limit of 10mg/m3.
Maintenance
Generally belt feeders require slightly more maintenance than screw feeders as the belt itself may require changing and the internal elements of the weighing system, the conveyor mechanism and belt drive rollers are all exposed to the product being fed. With a screw feeder, typically you only have the stainless steel walls of the hopper and feed trough, the feeder screw or screws and possibly an agitator blade in contact with the material. These are all typically 304 or 306 stainless steel and require little or no maintenance.
If the feeder needs regular cleaning then a belt feeder with suitable side panels allows for easy access to all of the internal components and can be stripped down.
Conclusion
Careful consideration of the entire materials handling system from the intake area through to the processing area will guide the correct feeder selection. If there are headroom constraints and high throughputs required, a gravimetric belt feeder may be the best option. Where rate are lower or only small amounts are being handle a screw feeder will offer excellent gravimetric control.
Our team would be more than happy to help and can arrange for product tests if there are any areas of concern. Please call or drop us a line via our contact page.