Bulk Material Discharge Devices
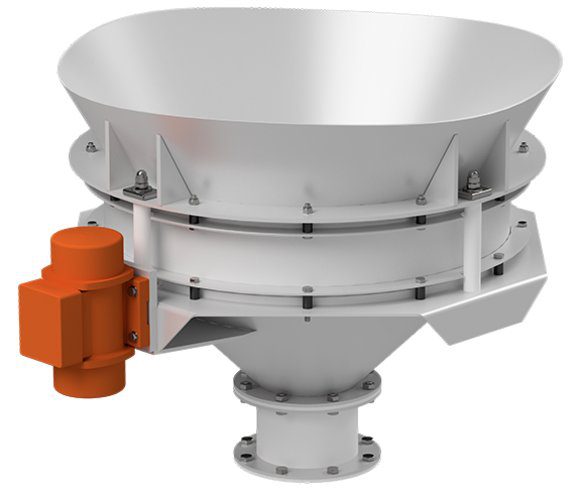
An Introduction to Discharge Devices
Bulk materials have to be stored before use, even if that is only for a relatively short period of time. When they are discharged from their silo, hopper, big-bag or sack tipping station, they will all flow in different ways. Some very easily and some only with a lot of encouragement. The design of this part of the materials handling system will have a significant impact on the downstream equipment.
Has the product become compacted whilst sat in the storage vessel? Just because it was flowing well when it entered the hopper, doesn’t mean that the same will be true when it comes to the time it has to discharge from it.
Environmental conditions will also play a part because the bulk material’s characteristics will change with temperature and moisture levels. This will particularly impact powders which may clump and become more solid.
Bulk Material Discharge Solutions
Genesis can offer you a wide range of storage and discharge devices and we have outlined the most effective ones below:
Sack tipping stations
Ideal for smaller ingredients that are supplied in sacks, the bag dumping station allows the operator to manually discharge several sack into a storage vessel that then feeders the downstream feeder or conveying system.
The system can include bin activators and other devices to help keep poor flowing materials moving; be fitted with integrated sieves to remove any large contaminants from the product stream and include dust control measures to keep the environment safe and any dust clouds controlled.
Outlets can be directly gravity fed into a pipe or be matched to a feeder or screw conveyor.
Example: Brabender Sack Tipping Station
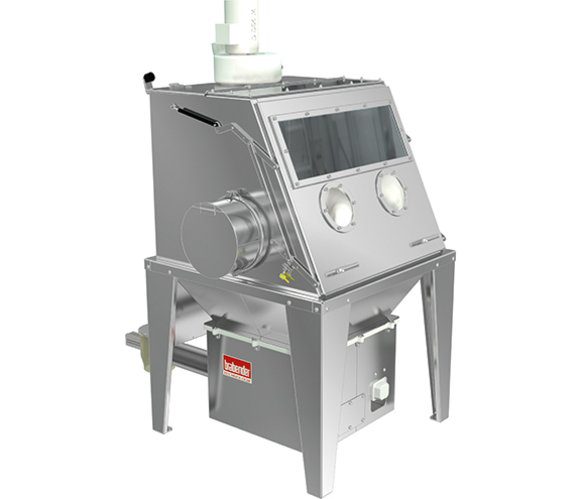
Big bag dischargers
When the material is delivered in semi-bulk containers, it will often be in a Big Bag. These require a properly designed big bag discharging station to support the bag as it empties and to interface correctly with the downstream device that is taking to product into the process.
Again, options can include simple hopper and valve arrangements to collect free flowing material as it exits the bag through to extensive bag “massaging” paddles that may be needed to move poor flowing product to the outlet.
Common options include load cells or level probes to indicate when the bag is empty, vibrating cones to aid product flow and various sealing arrangements to keep dusty products our of the environment.
There is no “standard” big bag discharger and the product flow from one material to the next will decide the complexity of the system required.
Example: Brabender Big Bag Discharger Above a Feeder
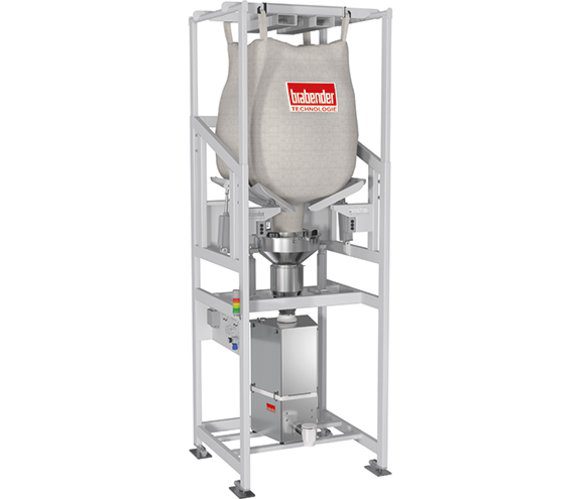
Bin activators
For products held in silos, a bin activation system is generally fitted out the outlet for all but the most free flowing or bulk materials. They can also be used to partially control the flow for very free flowing materials that would flood downstream devices if no measures were taken.
The silo design will play an important part in how the product flows out of it and where the product needs some assistance this can be either through vibration, air-pads, screw conveyor or a fully swept paddle the rotates around the inside such as our Prop-Flow discharger.
Example: Brabender Silo Tray Metering Bin Activator
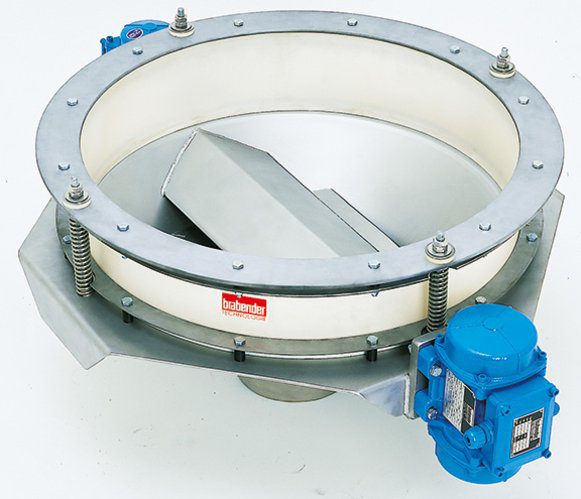
Prop Flow Discharger
The Genesis PROP-FLOW has been designed specifically for discharging flake and regrind from silos and hoppers.
As there is an increasing amount of pressure on customers to use more recycled & reclaimed material, the requirement for better handling systems has increased as well.
Flake and regrind material are both very abrasive and in most cases, poor flowing. Whilst the products can be conveyed, they don't flow well from hoppers and silos due to the nature of the product wanting to interlace and interlock together.
So a solution was required for hoppers and silos and after a long design process, the Prop-Flow range was born. The principal is simple, a flat bottomed discharger that uses a rotating blade - similar to that of a propeller - to move the material to an outlet whilst keeping the other material around it moving at the same time. The propeller causes a positive product displacement whilst the cone prevents any bridging in the centre of the Prop-Flow where there would normally be a dead spot.
Example: Inside and Underside of the Prop Flow Discharger
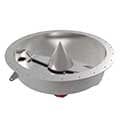
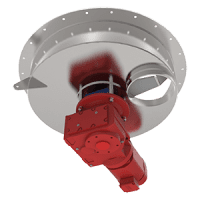
Flexible Silos
A flexible silo offers the ideal solution for many materials handling problems as the silo itself helps on the discharge of the product. As materials discharge the shape of the silo tends to change and creates a flexible cone that tends to prevent material from hanging in the outlet area.next will decide the complexity of the system required.
Example: Flexible Silo feeding conveying system with level sensor
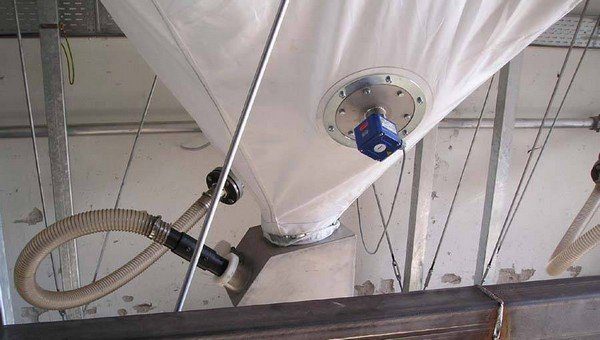
Further information
Genesis Process Solutions aims to provide the most reliable and effective materials handling equipment in the industry. If you would like to know more about our range of discharge devices or any of our other products or services, please use the details on our contact page.